End-of-line packaging can make or break your operations. It’s critical to ensure that every piece of your production process is running efficiently and consistently. The product cannot get shipped without being packaged and protected.
In fact, end-of-line industrial automation systems are no longer optional. They’re an absolute necessity to remain competitive and grow because every step in the supply chain requires protection, traceability and speed.
Let’s review what end-of-line packaging is, what type of equipment is available and how end-of-line automation can help you improve your packing line.
What Is End-of-Line Packaging?
End-of-line packaging is the final stage of the packaging process, where products are prepared and packed for storage, shipment, or retail display. Products are placed into their respective packages, such as cartons, cases, or pallets, and secured for transportation.
This process is critical to ensure products are protected during transportation and arrive intact at their final destination.
What Is End-of-Line Packaging Equipment?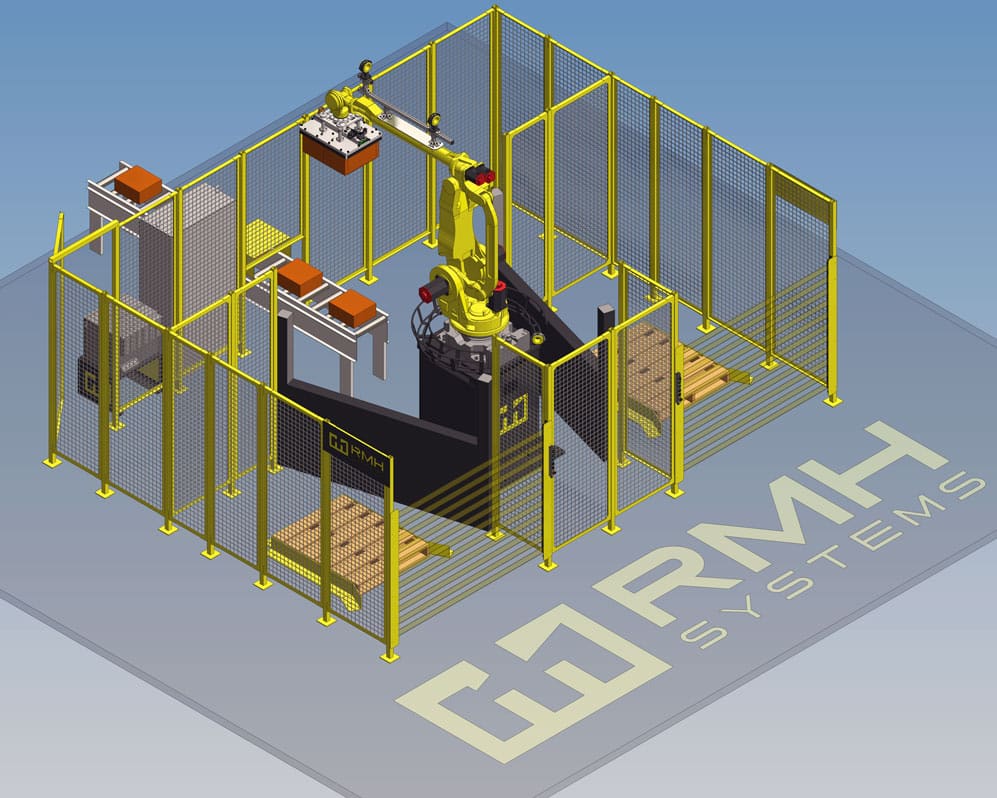
End-of-line packaging equipment refers to machines that prepare finished products for shipment or storage. This equipment is designed to automate or augment the final stage of the production process, reducing labor and increasing production output.
These machines perform tasks such as case-sealing, labeling, packing, palletizing and stretch wrapping. End-of-line packaging equipment includes:
- Conveyor systems
- Case erectors
- Case packing systems
- Palletizers
- Stretch wrappers
- Labeling machines
- Bagging machines
- Filling machines
- Strapping and banding systems
- Product traceability and coding systems
End-of-line packaging equipment can be manual, semiautomatic or fully automatic, such as a robotic palletizer.
How Can I Improve My Packing Line?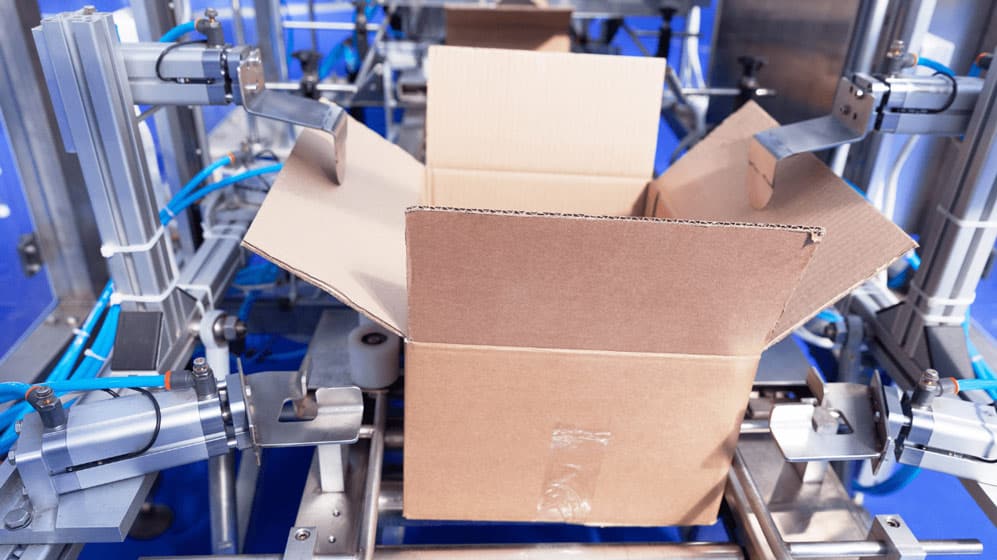
There are several ways to improve your packing line. By implementing these strategies, you’ll be able to enhance operational efficiency, improve product quality and increase customer satisfaction.
Automate Your Processes
Consider investing in end-of-line packaging equipment to automate your packing process. This can help to increase efficiency, reduce labor costs and improve overall productivity.
When considering automation, there are a couple of important factors to consider:
- Do you want to move products more quickly? In this instance, a cobot or industrial robot may be a good fit for your operations, rewarding you with speed, consistency, and no downtime, if your lines allow for it. Additionally, if your operations include track and trace for food or beverages, automated printing, and application speeds up the process while saving on labor costs.
- Do you need a less expensive option or a faster return on investment? If you’re a smaller company looking to begin automating and need a quick return on your investment, our experts typically recommend a pallet stretch wrapper. If you’re using it to replace manual labor and wrapping more than two pallets in a day, your ROI is typically under two years. Automating case forming, packing and sealing is another area where you can receive a quick ROI when replacing manual labor.
- Do you want a better shelf presentation? Automation rewards you with consistency each and every time, which means less shaking, less jarring and less damage to products.
- Do you need to trace products? Lot and date coding provides information on the product displaying the exact second it comes off the line and allows you to identify the sources of the materials included in a particular lot code.
Standardize Your Procedures
Develop standard procedures for packing and train employees on how to follow them. This helps to ensure consistency and accuracy, reducing the risk of errors and damaged products.
Optimize Your Layout
A company specializing in warehouse optimization consulting can help you arrange your packing line in a way that minimizes movement and maximizes efficiency. This may include repositioning equipment or workstations, optimizing material flow, and using industrial ergonomic equipment to safely lift, tilt and assemble while reducing the risk of injuries.
Conduct Regular Equipment Maintenance
Regularly inspect and maintain your packaging equipment to ensure it’s working properly. This reduces downtime, minimizes repair costs and extends the life span of the equipment. When choosing a partner, look for factory-trained packaging service technicians.
Monitor Key Performance Indicators
Track metrics such as cycle time, throughput and Overall Equipment Effectiveness (OEE) to identify areas for improvement and optimize performance. Coding, making and vision systems also provide traceability throughout the supply chain.
Automate and Grow Your Operations with RMH Systems
Partnering with the right packaging automation company is key to your company’s continued growth. RMH Systems has more than 80 years of experience in helping companies of all sizes work more efficiently and safely through our automation solutions.
Request a free, no-pressure engineering consultation and learn how we can help your team think through process flow optimization with material handling design and integration, packaging and robotic automation solutions.